Firetube Boiler Design: Engineering Efficiency and Reliability for Industrial Applications
The firetube boiler design has long been a cornerstone of industrial steam generation, celebrated for its simplicity, durability, and adaptability to diverse operational demands. At its core, this system channels hot combustion gases through tubes immersed in water, transferring heat to produce steam efficiently. Unlike water-tube alternatives, the firetube boiler design prioritizes compactness and ease of maintenance, making it ideal for applications where space and operational continuity are critical. Its inherent robustness allows for stable performance under fluctuating load conditions, while advancements in materials and combustion technology have further enhanced its thermal efficiency. As industries seek equipment that balances cost-effectiveness with consistent output, the firetube boiler design remains a trusted solution. Among the leaders harnessing this legacy is ZOZEN BOILER, whose WNS series exemplifies how modern engineering can elevate traditional firetube principles to meet contemporary industrial needs.
ZOZEN’s WNS Series: Innovations in Three-Pass Firetube Boiler Design
ZOZEN BOILER’s WNS series represents the pinnacle of three-pass firetube boiler design, integrating advanced engineering with practical enhancements to deliver superior performance. The system’s three-pass configuration ensures that flue gases traverse through precisely dimensioned tubes in three sequential phases, maximizing heat absorption while minimizing energy loss. This design is complemented by a corrugated furnace structure, which increases the surface area exposed to combustion gases, enhancing thermal conductivity without compromising structural integrity. The corrugation also accommodates thermal expansion, reducing stress on critical components and extending the boiler’s service life.
A defining feature of the WNS series is its optimized combustion chamber, which balances turbulence and retention time to ensure complete fuel burn. By precisely calibrating air-fuel ratios and employing advanced burner technology, the system achieves near-complete combustion, reducing unburned carbon residues and improving overall efficiency. The integration of high-efficiency threaded smoke tubes further amplifies heat transfer, extracting additional energy from flue gases before they exit the stack. These innovations collectively push thermal efficiency beyond 98%, significantly outperforming conventional firetube boilers and translating into measurable cost savings for industrial users.
Safety and operational flexibility are also embedded into the WNS series’ architecture. The boiler’s automated control system dynamically adjusts combustion parameters to maintain stable steam output, even under variable demand. Redundant safety valves, real-time pressure monitoring, and fail-safe shutdown protocols ensure compliance with international standards such as ASME and ISO certifications. Additionally, the system’s ability to operate on multiple fuel types—from natural gas to light oil—provides industries with the adaptability to respond to fluctuating fuel markets without sacrificing performance.
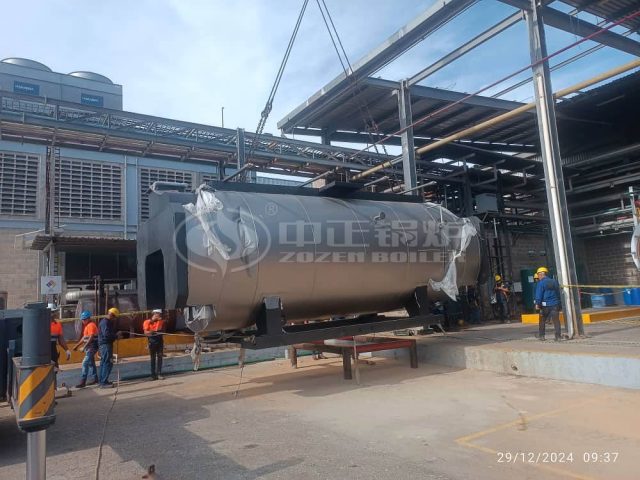
ZOZEN 10 ton WNS firetube boiler
Delivering Precision and Reliability for a Venezuelan Meat Processing Plant
ZOZEN’s expertise in firetube boiler design was recently demonstrated through a project with a large meat processing facility in Venezuela. The plant, which specializes in the production of preserved and ready-to-eat meat products, required a reliable steam source to power its processing lines. Key operations such as sterilization, cooking, drying, and packaging demanded consistent steam supply at precise temperatures to ensure product quality and food safety. After evaluating multiple suppliers, the company partnered with ZOZEN BOILER to install two WNS series gas-fired steam boilers—a 5-ton unit and a 10-ton unit—tailored to meet the plant’s dual-line production requirements.
The firetube boiler design of the WNS series proved instrumental in addressing the plant’s operational challenges. The three-pass configuration ensured rapid and uniform heat transfer, enabling the boilers to maintain stable steam pressure even during peak production hours. The corrugated furnace and threaded smoke tubes maximized thermal efficiency, reducing fuel consumption while sustaining high output levels. For the meat processor, this translated into lower operational costs and improved batch consistency, directly enhancing profitability.
Compliance with international safety standards was another critical factor. Both boilers were manufactured to meet ASME certification, a globally recognized benchmark for boiler safety and quality. This certification not only assured the plant’s adherence to local regulatory requirements but also positioned it to explore export opportunities in markets with stringent quality controls. The integration of ZOZEN’s automated control system further minimized manual intervention, allowing operators to focus on production rather than boiler management.
Post-installation, the meat processing facility reported significant improvements in both efficiency and reliability. The consistent steam supply also enhanced product texture and shelf life, reinforcing the plant’s reputation for quality. By adopting ZOZEN’s firetube boiler design, the company secured a competitive edge in a demanding market while laying the groundwork for future expansion.
Broad Applications and the Value of Post-Sales Support
The versatility of the firetube boiler design makes it applicable across a wide range of industries, from food and beverage manufacturing to chemical processing and textile production. Its ability to deliver stable steam at varying capacities suits operations requiring precise thermal control, whether for sterilization, distillation, or power generation. For small to medium-scale enterprises, the WNS series offers a scalable solution that aligns with growth trajectories without necessitating major infrastructure overhauls.
Beyond technical excellence, ZOZEN BOILER distinguishes itself through its comprehensive after-sales support, ensuring that clients derive maximum value from their investments. A global network of service engineers provides on-site installation guidance, performance optimization, and preventive maintenance, minimizing disruptions and extending equipment lifespan. Remote diagnostics and real-time troubleshooting further enhance operational continuity, allowing clients to address potential issues before they escalate. This commitment to customer-centric service underscores ZOZEN’s role as a partner in long-term industrial success.
Elevating Industrial Performance Through Firetube Boiler Innovation
While the firetube boiler design may appear rooted in tradition, its evolution reflects a dynamic response to modern industrial demands. By combining time-tested principles with cutting-edge engineering, ZOZEN BOILER’s WNS series demonstrates how innovation can transform efficiency, reliability, and cost-effectiveness. For businesses seeking to optimize production while maintaining operational resilience, these boilers represent a strategic investment in sustainable growth.
To discover how ZOZEN’s firetube boiler solutions can enhance your operations, contant us. Explore tailored designs and expert support engineered to turn your energy challenges into opportunities—one steam cycle at a time.
Leave a Reply